**construction technology
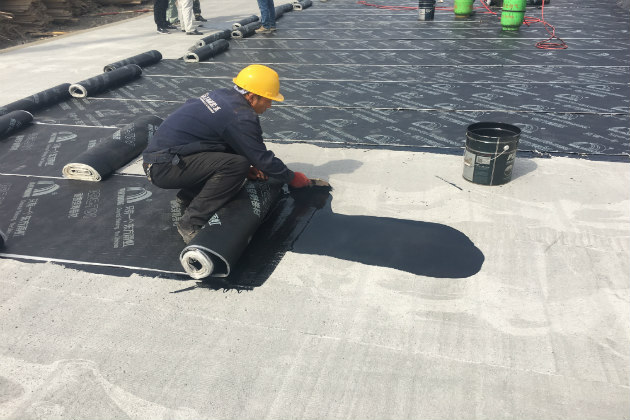
1. The overall paving sequence of the membrane is:
first high span, after low span; equal height, first far and then near; the same facade, paving from high to low.
2. Base Coat:
After cleaning and acceptance of the base surface, apply the special primary treatment agent uniformly to the base surface. When brushing, press one direction, the thickness is uniform, don’t leak the bottom, don’t pile up, Put it to the point where it doesn't stick.
3, Spring line and test paving:
In the bottom coating, according to the actual lap area, pop up and paste the control line, and strictly press and paste the control line and the actual bonding material , to ensure that the width of the membrane is 6 ~ 7cm (marked on the membrane). According to the characteristics of the site, determine the density of the bullets to ensure that the membrane are kept straight and sticking will not occur due to accumulated errors. The membranes should be tried and put in place first, and then correctly cut the shape according to the required shape before starting the actual adhesion.
4, Node processing:
(1) Parapet wall treatment :
When making cement mortar, it is necessary to apply a small radius with a radius of about 50mm to the inside corner of the wall and the roof. After the base surface meets the requirements, First apply a polyurethane waterproof layer, apply a layer of carcass reinforcement (glass fiber cloth) immediately after brushing, and then apply a second polyurethane waterproof layer to bond firmly with the base surface, also easy to self-adhesive membrane Construction.
(2) The treatment of yin-yang Angle and pipe mouth.:
The Angle of Yin and Yang should be made into a round corner of 50mm with mortar, and a waterproof additional layer shall be added together with a glass fiber cloth in the attached layer. , at the junction of nozzle and good leveling layer, the reserved grooves, filling sealing material, give around pipeline cleaning, polishing, nozzle area of around 500 mm will be waterproof additional layer, add a glass fiber cloth, to ensure the comprehensive waterproof effect.
5, large area of the membrane material:
There are two main methods for large area pasting self-adhesive rolling material, pulling and rolling. In actual construction, construction workers can determine the pasting method according to the conditions of the site environment, temperature, sunshine, etc., but basic exhausting and compaction Anti-wrinkle requirements are still the same.
(1) Basic requirements:
When sticking a membraneed material, it is necessary to pay attention to the alignment with the reference line at all times to avoid deviations that are difficult to correct. When membranes are applied, the membranes must not be stretched by force. After the paste, with roller from central membrane rolling in both sides, discharge the air, make membrane solid paste on the grassroots, membrane on the back of the overlapping parts of the isolated premature don't remove the paper, in order to avoid pollution bonding layers or sticky.
(2) Pulling method:
Spread the web to the full line of the reference line, lift the web (including the release paper) from one end, fold it along the long centerline of the web, and use the paper cutter to gently sever the edge of the paper. Open, take care not to scratch the web. Carefully tear the release paper from the back of the web to a length of about 500 mm. The two work together to peel off the release paper and align it with the base line. First spread the half-length membraneed material into place, pull the uncovered release paper evenly and forcefully pull it backwards, slowly pull out the remaining half-length of the release paper, and pay attention to the integrity of the extracted release paper when pulling the store. It was found that the tearing and breaking should be stopped immediately and the remaining scraps of tearing paper should be cleaned before continuing to pull.
(3)Rolling method:
That is, peeling the release paper and laying the web at the same time. Construction does not need to open the whole roll membrane, with a tube inserted into the center of the cylindrical membrane paper core barrel, and then carried by two people from steel tube end to spread position between, and about 500 mm, displaying membrane forward by another person lift isolation paper strip off this part of the membrane, and its volume to have used on the paper core. The membrane that has been stripped away from the paper is placed on the base of the bomb and then compacted. After the beginning of the spread, one person slowly uncovers the paper and pulls the paper into the paper cylinder, and then moves forward. The two men carrying the roll also roll along the base line along the base line. Note that the moving speed of the two moving materials should be the same and coordinated. Don't slack off when rolling; After finishing a roll, use a long handle roller brush, starting from the starting end, completely eliminate the air under the membrane, and then use a large roller or handheld portable vibrator to press the membrane compaction and paste firmly.
(4) Laying of facades and steep slopes:
Since the self-adhesive web has a relatively low adhesion to the base, the web tends to slide on the facade or on large slopes. Therefore, When pasting on a large slope, it is advisable to use a hand-held gasoline torch to properly heat the adhesive on the bottom of the membrane and then paste, vent, or roll.
(5) After the large area membrane exhaust, compaction, then use the hand small press roller to carry on the ground to be rolled, from the inside edge of the lap to roll pressure, the discharge air, paste solid.
(6) joint paste and seal:
Lap joint paste: self-adhesive roll overlap at the factory leaving a lap edge, when bonding only need to lift off the release paper, lap width is generally 6 ~ 7cm.
Laminated lap seals: The lap joints at the short side of the membrane, the membrane head, the pipe wrapping, and the shaped parts shall be sealed with a special sealing paste for self-adhesive rubber bitumen membranes. The lap joint seal width is not less than 10cm.
6. Fixed and closed head:
The end of the membrane is inserted into the groove (deep 20mm x height 40mm ~ 60mm trapezoid groove), the metal clamp is firm and sealed with special seal.
(1) The short side joints of the two adjacent rows should be staggered over 300mm, so as to avoid the overlapping of the multilayer joints and make the membraneed material unevenly. When the waterproof area is large, and the construction must be carried out in stages, there is a lot of temporary pick-up in the middle process, and a special sealant should be used for temporary closure.
(2) After the material is pasted, measures should be taken to temporarily cover, reducing the chance of damage caused by direct exposure. This paper can also be used as an insulating layer between the waterproof layer and the protective layer.
(3) After exposure, exposure to sunlight may cause slight surface wrinkles and blisters. This is a normal phenomenon and will not affect its waterproof performance. Once hidden, it will disappear.
(4) The waterproof layer should be concealed as soon as possible, and it should not be exposed for a long time. It should usually be concealed within 24 hours after the completion of the waterproof layer. If there is a closed water test, the concealment time shall be calculated from the end of the closed water test.
(sourcing: network)